Oil, Gas and Mining
Real-time equipment monitoring
Continuous Sensor Data Collection: CrateDB facilitates the continuous collection of sensor data from mining equipment, capturing metrics such as temperature, vibration, and operating conditions in real-time.
Instant Alerts and Notifications: CrateDB triggers instant alerts and notifications based on predefined thresholds or anomalies detected in sensor data. This enables mining operators to promptly respond to equipment malfunctions or deviations from normal operating conditions, minimizing downtime and preventing costly breakdowns.
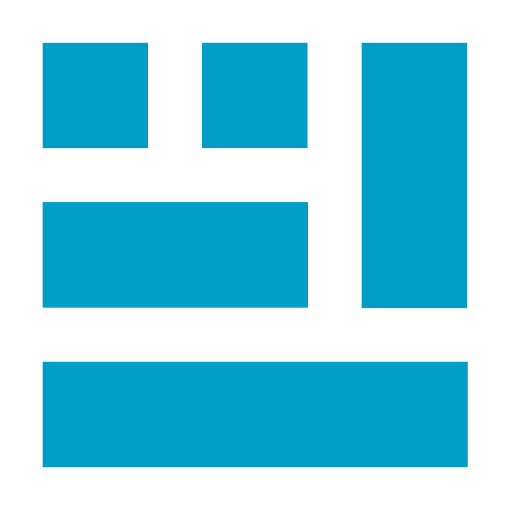
Predictive maintenance
Data-driven Equipment Health Analysis: CrateDB enables mining companies to collect and analyze historical and real-time data from sensors and equipment logs. By identifying patterns and trends in equipment performance, CrateDB can assess the health of mining equipment and predict potential failures.
Proactive Maintenance Scheduling: Based on the insights gained from data analysis, CrateDB helps mining companies schedule maintenance activities proactively. By identifying impending equipment failures before they occur, companies can plan maintenance interventions during scheduled downtimes, minimizing disruptions to production and reducing maintenance costs.
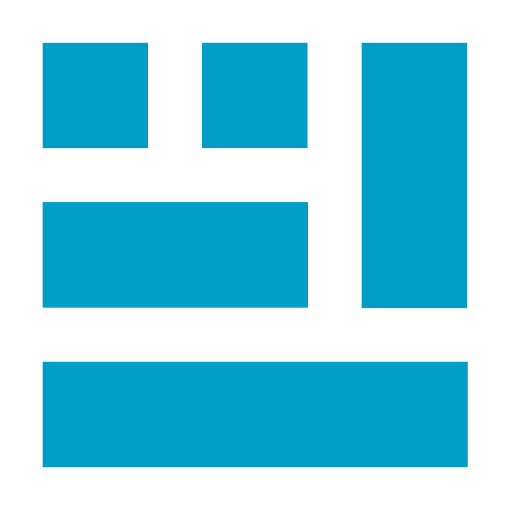
Safety monitoring and compliance
Integrated Sensor Data Analysis: CrateDB integrates sensor data from various safety monitoring systems, including air quality sensors, temperature sensors, and seismic monitoring devices. By analyzing this data in real-time, mining companies can assess safety conditions and detect potential hazards such as gas leaks or ground instability.
Regulatory Compliance Reporting: CrateDB enables mining companies to generate reports on safety metrics and compliance with regulatory standards. By aggregating and analyzing data on safety incidents, environmental conditions, and compliance measures, CrateDB facilitates regulatory reporting and ensures adherence to safety regulations in mining operations.
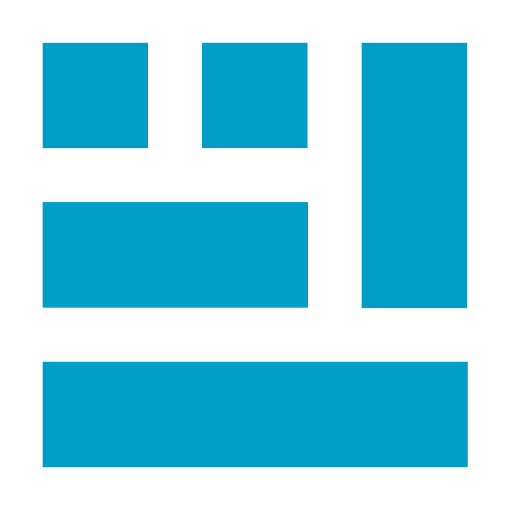
Case study: SPGo!
SPGo!, a part of PETROMIN, has revolutionized the mining industry by digitally inspecting conveyor belts using CrateDB, a database for all types of data, combining the simplicity of SQL and the scalability of NoSQL. The traditional manual inspection process was inefficient, inconsistent, and posed health risks to inspectors. SPGo! has developed applications that monitor conveyor belt idlers 24/7 using online sensors. These applications inspect the operating conditions of the equipment based on temperature, vibration, and humidity parameters. With a predictive algorithm, SPGo! alerts the client when to change specific equipment set to fail during their planned maintenance stops. This solution saves resources, manpower, costs, and losses due to downtime thanks to:
- Real-time component monitoring
- Predictive failure analysis
- Management of operations KPIs
Translating the solution into numbers
CrateDB empowers SPGo! to manage:
30,000 | 760 million | >80% |
sensors per mine | records per day | increase in data-driven predictive maintenance |
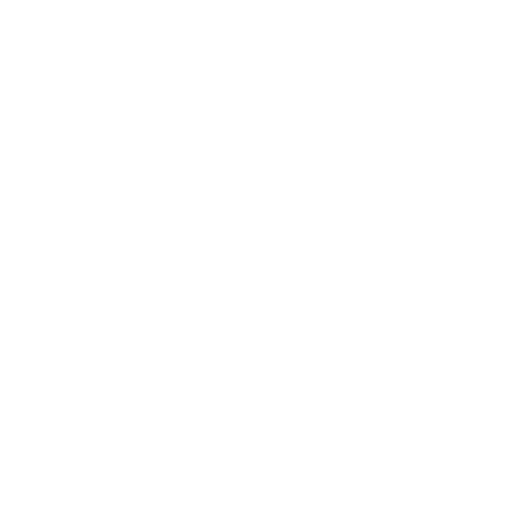