SPGo! - Real-Time Digital Inspection of Conveyor Belts in the Mining Industry
SPGo! is part of PETROMIN, which has more than 23 years of experience in the mining and oil industries.
At SPGo!, the objective is to improve the profitability of their clients' businesses in the mining industry by applying IIoT technology with a predictive maintenance model through the management of Big Data.
© SPGO!
The challenges
In the mining industry, companies have tried to predict potential issues with critical equipment without much success. SPGo! aims to change that.
Considering that mineral conveyor belts range from 1 to 15 kilometers, it is necessary to change the paradigm of equipment inspection currently carried out by people.
Currently, an inspector walks along the leash with thermal guns measuring and recording the temperature of the poles via photographs and paper. The process is manual, inconsistent and in the long run inefficient, which raises many issues including:
- Risk to the health of the people who inspect the running belt;
- Poor ability to prevent incidents, shutdowns, and failures in the future;
- The number of people that will be needed to monitor the entire leash;
- Additional costs for the workers such as services, food, work clothes, transportation, equipment;
- The quality and accuracy of the information recorded and passed to the database manually;
- The overall cost of operation lost due to an unscheduled stop of the belt
For SPGo!, the challenge has been to build digital tools using technologies that allow timely analysis based on large amounts of data and wireless hardware with high autonomy that can operate under adverse environmental conditions. SPGo! is in a position to deliver a robust solution to its customers with real-time component monitoring, predictive failure analysis, management of operations KPIs, task fulfillment, maintenance plans and much more.
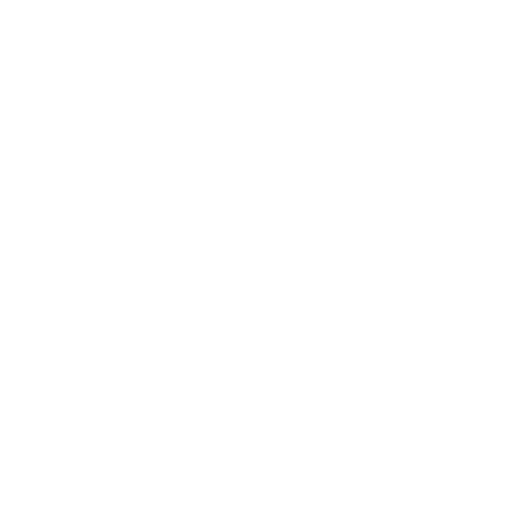
Translating this challenge into numbers
To SPGo!, it is in these numbers that CrateDB shows its power.
-
More than 30,000 sensors per mine, data ingested
-
760 million records/day, managed data
-
80% increase, data-driven predictive maintenance
The solution
SPGo! builds applications for monitoring all material conveyor belt idlers (24 hours a day at every minute) through online sensors. The applications enable workers to inspect the operating and working conditions of the equipment according to temperature, vibration, and humidity parameters.
By using a predictive algorithm, SPGo! alerts the client when to change which specific equipment (that is set to fail) in their planned maintenance stops. This helps the mining customer save resources, manpower, costs and losses due to downtime.
When SPGo! was looking for a solution, there were two key features that convinced them to go with CrateDB:
- The speed response for Big Data management;
- CrateDB does not require an internet connection, offering the freedom and reliability to host data locally without sending the data to an external cloud service.
As a result of this, there's a better response time and SPGo! is able to avoid the delay that can occur when data is sent off the network.
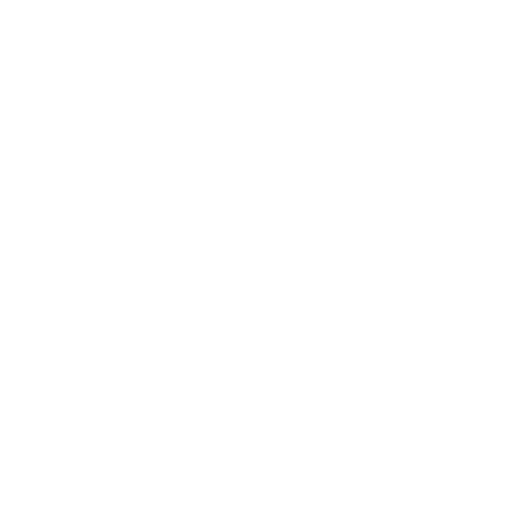
Translating the solution into numbers
To SPGo! CrateDB empowers them to manage:
30,000 | 760 million | >80% |
sensors per mine | records per day | increase in data-driven predictive maintenance |
Why CrateDB?
SPGo! chooses and continues to use CrateDB because it is very easy to use from installation to querying. There is no need for a complex architecture or advanced knowledge of SQL to start getting the right results. It has many integrations with other platforms, which makes the implementation quick and smooth.
According to SPGo!'s Head of IT Development and Projects, Nixon Monge Calle, there are several reasons to prefer CrateDB over alternative options:
- CrateDB's writing and reading speeds are incredibly fast which made it possible for them to get the necessary immediate answers;
- While entering data into CrateDB, they observed no bottlenecks or other "surprises" that caused a loss of information;
- Resource consumption is low and servers can work comfortably with CrateDB;
- The ability to configure multiple clusters behind a load balancer with CrateDB gave them the flexibility to build an environment according to the demands of data collection;
- CrateDB's scalability ensures that they maintain optimal performance of their systems;
- The stability of CrateDB provides them the confidence to complete their work and that dependability can be transferred to their customers.
Furthermore, it is a database that meets all the needs of the large-scale deployment of an application.
- High vertical scale and flexibility;
- High performance that supports large data intakes;
- Freedom to configure work environments according to specific needs or requirements;
- The use of SQL allows IT and support teams to manage the database effortlessly.
While looking for a solution, SPGo! was exploring other databases
They tried the most popular ones on the market. Some were disqualified due to excessive delay in their responses to make inquiries. Other databases forced SPGo! to send the data out of the work environment and this influences the overall speed of the system. They were using MongoDB and after a few months they switched to CrateDB.
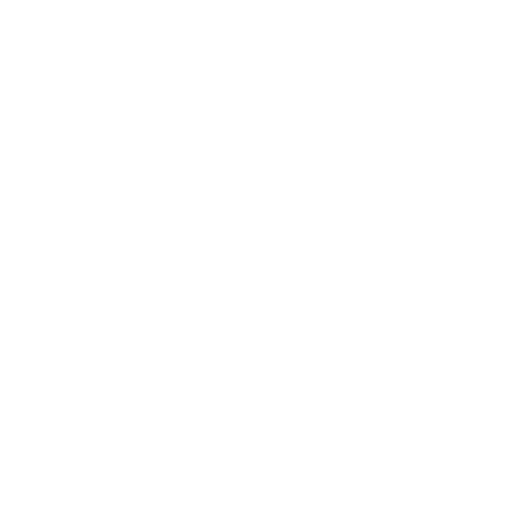
What are the real benefits?
As indicated by the saying "time is money", SPGo!’s solution aims to help convert the events of "unscheduled stops" to predictive maintenance. The goal is to redirect the identified failures proactively to the times of the "scheduled" plant shutdowns, which increases the performance and service life of components; translating into an improved return on investment of expensive mining equipment. In turn, this also helps the mining company guarantee the availability of materials transported to its customers.
Learn more about CrateDB. Have more questions? Talk to our team, we will be happy to help you!
How SPGo! builds apps for monitoring and predictive maintenance
In this webinar you will hear about real-time component monitoring, predictive failure analysis, management of operations KPIs and how it helps mining businesses save resources, workforce, and losses due to downtime.
