ALPLA: Analyzing Sensor Data in Real-Time to Increase Factory Efficiency
ALPLA is a world leader in the area of packaging solutions, producing high-quality packaging for Coca-Cola, Unilever, and other brands in the food, drinks, cosmetics and cleaning industries. ALPLA employs 20,900 employees at 181 locations across 46 countries.
As the complexity of production machinery increases, so does the need for highly trained specialists in each factory. This creates the following challenges:
- Higher personnel costs in every plant
- Harder to recruit experienced talent at each location
- Personnel turnover becomes more costly
- Less experienced operators run the machines sub-optimally, impacting resource consumption and overall equipment effectiveness (OEE).
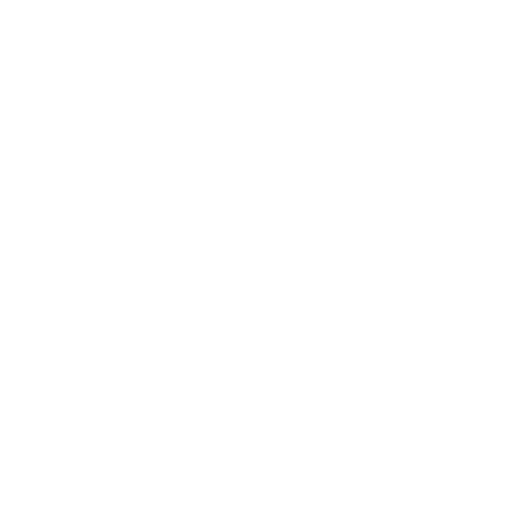
Inform "Mission Control" with real-time factory floor data
“We are running visual inspection systems in about every line of our plants. Having people constantly monitor these systems on the factory floor and reacting to any error is almost impossible,” said ALPLA General Manager, Jodok Schaeffler.
In 2016, ALPLA used manufacturing machinery data to help solve these problems. Each factory had 900 different types of embedded sensors.
Data from the sensors was used automate the machines in real-time, telling them when to eject defective products and informing nearby operators on the factory floor about equipment performance, which they could then tune and optimize.
The big idea at ALPLA was to integrate sensor data from multiple factories and production lines into a central “mission control,” staffed by experts who monitor production via interactive dashboards. Those centralized experts could give direction to less experienced, lower-cost factory workers.
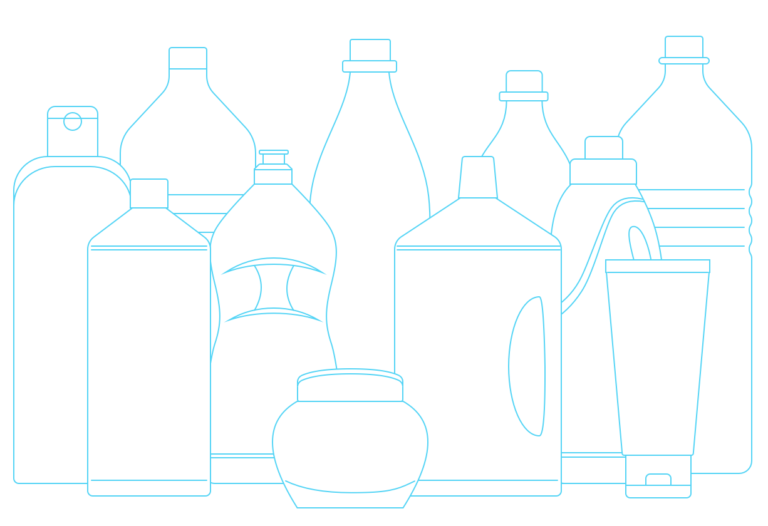
ALPLA produces plastic packaging for leading brands.
A challenging use case for traditional SQL
ALPLA initially chose SQL Server as the data store for the sensor data, but it was unable to cope with their data requirements. They needed 900 different tables, one for each of the 900 different sensor data structures. Each production line generated thousands of readings per second.
Trying to query streams of that volume of sensor data in real time, and running complex machine learning analytics on terabytes of historic data, was outside of SQL Server’s sweet spot. Charts in the mission control dashboards were taking 3 to 5 minutes each to update, which was prohibitively slow since each dashboard contained a dozen or more charts.
The switch to a solution powered by CrateDB: 250x faster...
ALPLA switched to CrateDB, perfectly suited for IoT workloads. That was attractive for the following reasons:
- SQL: Easy to migrate data and code to CrateDB from SQL Server
- Dynamic schema: Allowed ALPLA to combine all their 900 different sensor readings into a single table for easier maintenance and faster querying
- Distributed: Easy and economical to scale on elastic clusters of inexpensive servers
- Real-time performance: Columnar indexes cached in memory enable the solution powered by CrateDB to execute dashboards queries 250x faster than SQL Server (in milliseconds, not minutes)
The final result - improved factory efficiency
With mission control now centralized and monitoring production efficiency 24x7, ALPLA can benefit as follows:
- Lower personnel costs by requiring fewer experts
- Perform cross-plant analysis to get new insights
- Get immediate insight and control instead of next-day quality reporting
- Improve OEE